- Регистрация
- 26 Фев 2017
- Сообщения
- 380
- Реакции
- 176
- Баллы
- 43
ОТ ДРЕВНЕГО ЕГИПТА ДО СЕРЕДИНЫ ХХ ВЕКА
Фанера была известна людям еще на заре цивилизации. Самый старый, полуистлевший кусок фанеры, относящийся примерно к 2600 г. до н. э., найден в Египте в одной из усыпальниц члена семьи фараона третьей династии Джосера. Алебастровый саркофаг был обшит изнутри шестислойной фанерой. Слои древесины толщиной 4 мм скреплялись деревянными гвоздиками и чрезвычайно плотно прилегали друг к другу. Как и в современной фанере, расположение слоев было взаимно перпендикулярным!
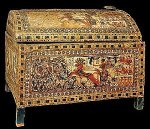
Ларец из гробницы Тутанхамона. Египет, 1332 год до н. э
Судя по найденным в Египте артефактам, начиная с 1750 года до н. э. технология фанерования получила широкое распространение. В Египте того времени не было ни больших лесов, ни высоких деревьев. Местные акация, можжевельник, платан и деревья других пород с древесиной в основном низкого качества могли распиливаться только на небольшие доски. Ценимое египтянами черное дерево ввозились из Восточной Африки, а кедр и сосна – из Ливана. Стоимость древесины была очень высокой, именно это в конечном счете и заставило древних мастеров использовать технологию фанерования. Производство было очень трудоемким – слои фанеры изготавливались вручную путем продольной распиловки стволов тонкими (0,5–1,5 мм толщиной) медными пилами с треугольными зубьями. В найденных произведениях искусства египетских краснодеревщиков толщина слоев древесины составляла менее 3 мм, и они уже были соединены клеем. Этот клей изготавливался из содержащих желатин продуктов животного происхождения: костей, кож, сухожилий и хрящей.
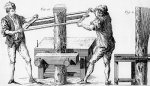
Изготовление шпона пилением. Европа, начало XVII века
Впоследствии метод фанерования стали использовать в Древнем Риме и Греции. Известно, что и древние китайцы применяли подобную технику при производстве мебели. В этих странах так же, как и в Египте, постоянно ощущался дефицит древесины ценных пород. Она завозилась издалека и была очень дорогой.
Значительно позже технологию производства фанеры освоили в Европе. Мебель, изготовленная французскими мастерами в XV–XVI веках для украшения королевских и дворянских замков, очень часто фанеровалась тонкими дощечками из ценных и редких пород красного и черного дерева. Подобная мебель стоила немало, но все-таки была дешевле изготовленной из цельной древесины, поэтому пользовалась большим спросом и была доступна среднему классу нарождающейся буржуазии. Со временем появилась необходимость в совершенствовании технологии и оборудования производства фанеры, так как вплоть до конца XVIII века шпон изготавливали вручную, а потому цена фанеры была высокой, а ее качество оставляло желать лучшего.
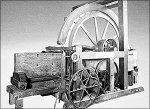
Станок братьев Мундинг для изготовления шпона пилением. Австрия, 1800 год
Попытки механизировать процесс производства шпона предпринимались еще в начале XVIII века. Первый английский патент, относящийся к производству шпона, был предоставлен в 1635 году Саре Джером и Уильяму Уэббу, за «двигатель для резки древесины в тонкие чешуйки» для изготовления бандажей, ножен для мечей и т. п.
Однако, несмотря на то что производство фанерованной мебели значительно выросло и требовалось все больше качественного шпона, период с 1700 по 1830 год был временем расцвета ручного пиления и использования ручного резака для получения шпона.
Растущий спрос на декоративную мебель состоятельных аристократов, среднего класса и священнослужителей крупных городов в XIX веке привел к изменениям в технике для изготовления шпона.
В Вене того времени было много богачей, которые хотели обставить свои дома мебелью, изготовленной из шпона ценных пород древесины, и австрийцы Алоис и Мартин Мундинг еще в 1800 году стали использовать машину для резки шпона. Этот деревообрабатывающий «бегемот» имел длину 6 м и высоту более 3 м. Двое рабочих управляли им с помощью педалей. При изготовлении шпона на таком станке древесная стружка и опилки составляли четверть или даже половину первоначального объема распиливаемой заготовки.
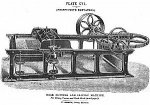
Горизонтальный строгальный станок Арбея. Франция, 1875 год
В 1806 году выдающийся английский инженер французского происхождения Марк Исамбард Брунель получил британский патент на строгальный станок с ручным приводом. Этот станок стал прообразом современных строгальных станков с горизонтально движущимся ножом. Станок хорошо резал прямослойную древесину красного дерева, но при строгании плотного палисандра потерпел полное фиаско. В дальнейшем Брунель отказался от принципа изготовления шпона строганием, сосредоточившись на создании станка для раскроя древесины с помощью циркулярной пилы сегментного типа. Разработанный им станок, оснащенный паровой машиной мощностью 16 л. с., позволял распиливать доски из красного дерева и палисандра на шпон толщиной всего 1/16 дюйма (1,6 мм). Станки Брунеля успешно использовались на заводах по производству шпона по всей Великобритании. На некоторых заводах было установлено больше десятка станков с пилами от 7 до 17 футов в диаметре! Производительность подобного оборудования была невысокой, так как скорость подачи не превышала четверти фута в секунду.
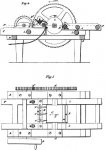
Лущильный станок, разработанный Генри Хамфри. США, 1842 год
К идее изготовления шпона способом горизонтального строгания в 1875 году вернулся французский изобретатель Арбей. Разработанные им станки позволяли изготавливать шпон толщиной 1/100 дюйма, качество поверхности было таким высоким, что шлифование не требовалось.
Однако настоящий прорыв в технологии производства фанеры был сделан только после изобретения технологии резания вращающегося бревна (чурака) ножом, движущимся поступательно к оси вращения. Общепризнанный приоритет технологии роторной резки шпона или лущения – за российскими инженерами начала XIX века. В отчете, опубликованном в Великобритании в 1817 году, было сказано, что российский изобретатель в Санкт-Петербурге сделал станок, который производит «листы фанеры около ста футов в длину и четыре, пять или даже больше в ширину».
Похожую машину в Англии в 1818 году запатентовал Генри Фаверир. О практическом применении машины Фаверира ничего не известно. Через некоторое время подобный станок был разработан в США и как «улучшенный роторный резак шпона, приводимый в движение паром», использовался промышленником Ричардсоном в Филадельфии в 1825 году.
Интересно, что конструкция и узлы современных лущильных станков по сути идентичны конструкции и узлам станков, разработанных еще в середине XIX века. Например, на рисунке к патенту, выданному в 1842 году Генри Хамфри, можно видеть подвижный суппорт с закрепленным ножом, обжимной и поддерживающий ролики, подрезные ножи и т. д.
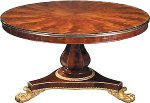
Стол из фанеры, облицованной шпоном махагони. Франция, XIX век
В 1843 году в энциклопедической статье (Penny Cyclopedia, 1843) резка шпона описывалась так: «В России с помощью строгальной машины изготавливают шпон, который настолько тонок, что может использоваться для книжных переплетов, причем лента шпона сто футов в длину была нарезана этой машиной в течение трех минут».
Лондонский журнал Mechanic’s magazine в статье, опубликованной в 1848 году, отмечал значительное преимущество роторной резки по производительности перед другими способами изготовления шпона. В статье описывалась машина, которая могла нарезать рулон кленового шпона длиной 300 футов и шириной 3 фута из бревна диаметром 20 дюймов.
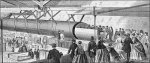
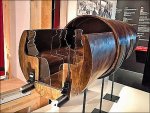
Прототип подвесной железной дороги Альфреда Эли Бича, изготовленный из фанеры. США, 1867 год вверху – общий вид; снизу – вагон, вмещающий 10 пассажиров
Однако технология роторной резки шпона получила признание не сразу. Автор словаря производств Джордж Додд в 1860 году писал: «Хотя при изготовлении шпона в Англии пилами Брунеля расходуется больше древесины, этот способ дает более качественный шпон, чем роторный метод, получивший распространение на континенте».
Повышению качества шпона роторной резки способствовало внедрение предварительного замачивания бревен для смягчения древесины. Вероятным новатором был француз Гаранд, придумавший этот метод в 1860 году. Вскоре замачивание, в том числе и в горячей воде, стало применяться повсеместно, хотя и влияло на цвет шпона.
Споры о качества шпона, получаемого различными способами, продолжались во второй половине XIX века. Известный английский инженер Чарльз Хольцзаффель предположил, что шпон, полученный роторной резкой, будет скручиваться и расщепляться. С другой стороны, корреспондент издания Universal Decorator отмечал, что шпон, полученный лущением, вызовет настоящий бум производства мебели.
Считается, что первый патент на фанеру в том виде, в каком она выпускается сегодня, был выдан Джону К. Майо в 1865 году. Однако сделанное им изобретение кануло в Лету, так как Майо не пытался получить коммерческую выгоду от его использования.
Машинное производство шпона позволило значительно снизить стоимость фанеры, многократно повысить качество материала, которое существенно превосходило качество фанеры ручного изготовления и выпускать мебель по доступным ценам.
Хотя в те времена фанера использовалась преимущественно для изготовления мебели, были и попытки применять ее в весьма необычных проектах. Так, удивительно смелая даже по нынешним временам идея построить в Нью-Йорке пневматический надземный метрополитен пришла в голову богатому бизнесмену и изобретателю Альфреду Эли Бичу, своего рода Илону Маску того времени. Он планировал протянуть подвесную дорогу по всему городу на столбчатых опорах либо прикреплять ее к стенам зданий. Прототип дороги длиной 107 футов в виде формованной фанерной трубы был продемонстрирован в 1867 году в большом выставочном зале американского института в Нью-Йорке. Установленные на обоих концах трубы гигантские вентиляторы создавали напор воздуха достаточный для того, чтобы посетители выставки могли ездить внутри трубы в цилиндрических вагончиках, также изготовленных из фанеры и вмещающих десять человек, туда и обратно.
Несмотря на очевидные достижения как в области оборудования и технологии производства, так и в применении, популярным строительным материалом фанера стала только в начале 1900-х годов, чему в немалой степени способствовала всемирная выставка 1905 года в американском Портленде. В этом городе был один из первых фанерных заводов США Portland Manufacturing. Владелец завода Густав Карлсон изготовил несколько образцов фанеры из местных хвойных пород, используя для нанесения клея малярные кисти, а для прессования автомобильные домкраты. Новый материал вызвал большой интерес у производителей дверей, легковых автомобилей и грузовиков, строителей. Заказы потекли рекой. К 1907 году компания установила станок для нанесения клея и ручной пресс. Производство выросло до 420 листов фанеры в день.
Наиболее технологически значимой сферой применения фанеры с 1910 по 1945 год стало самолетостроение. Прочность и легкость материала позволили проектировать и изготавливать принципиально новые, прогрессивные для того времени конструкции самолетов.
Еще в начале 1910 годов новаторские эксперименты с формованной фанерой позволили построить первый закрытый, обтекаемый фюзеляж самолета – монокок (от фр. мonocoque, означает «единая оболочка»), ставший тогда стандартом в конструировании самолетов.
Фюзеляж, сделанный по принципу монокока, состоял из внешней оболочки, изготовленной из фанеры, форма которой удерживалась несколькими внутренними поперечными переборками. Революционный по тому времени монокок, конструкция которого была несущей, имел гладкую обтекаемую форму, отличался прочностью, жесткостью и легкостью. Французский инженер Луис Бекеро в 1911 году впервые использовал фанерную монококовую конструкцию в фюзеляже гоночного моноплана Deperdussion.
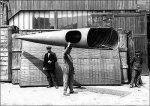
Фюзеляж истребителя SPAD-Deperdussin представлял собой конструкцию в виде монокока, выклеенного из фанеры, и настолько легкую, что его мог спокойно переносить один рабочий. Франция, 1913 год
Позже конструкцию фюзеляжа в виде монокока из фанеры использовали авиастроители при создании самых известных и скоростных истребителей Первой мировой войны Bleriot-SPAD, Albatross D-III.
В 1930-е годы в СССР, испытывавшем острый недостаток алюминия, фанера также широко использовалась в авиастроении. Отечественные инженеры создавали из фанеры самолеты оригинальных, новаторских конструкций.
В 1928 году в Ленинградском институте инженеров путей сообщения, в студенческом самолетном кружке, возглавляемом В. Ф. Рентелем, возникла мысль построить опытный самолет из фанеры. Широкое применение фанеры в конструкции с обусловило второе название самолета: «Фанера-2». Построенные небольшой серией эти самолеты успешно эксплуатировались на местных линиях Аэрофлота, в Арктике и на Дальнем Востоке.
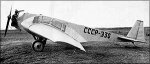
Самолет «Фанера-2», изготовленный почти целиком из фанеры. СССР, 1933 год
Фанера широко использовалась при создании боевых самолетов времен Второй мировой войны. У британского de Havilland Mosquito (DH-98), одного из самых известных самолетов того времени, был формованный фанерный фюзеляж-монокок – легкий и обтекаемый. Поэтому даже с довольно маломощными моторами он был настолько быстрым, что летал без оборонительного вооружения. Немецкие истребители ПВО просто не могли его догнать.
Интересно, что министерство авиации Великобритании хотело, чтобы на вооружение поступил самолет, изготовленный из металла, и первоначально отвергло проект. Однако конструкторы фирмы de Havilland Aircraft Company доказали, что можно создать технологичный и дешевый самолет из фанеры, используя неквалифицированный труд работников мебельных и деревообрабатывающих заводов в Великобритании, Австралии и Канаде.
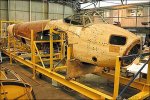
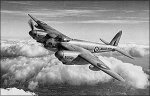
Самолет de Havilland Mosquito (DH-98). Великобритания: вверху – фюзеляж-монокок из фанеры на стапеле в процессе реставрации; внизу – самолет в полете
Самым ярким примером использования фанеры в самолетостроении является транспортная летающая лодка Hughes H-4 Hercules, разработанная американской фирмой Hughes Aircraft под руководством Говарда Хьюза в 1947 году. Этот гигантский 136-тонный самолет первоначально получил прозвище Spruce Goose (дословно «Еловый гусь»). Несмотря на «хвойное» название, самолет был почти полностью построен из выклеенной по шаблону березовой фанеры. H-4 – самая большая из когда-либо построенных летающих лодок, размах ее крыла – 98 м оставался рекордным для самолетов до 2017 года. Для сравнения: у ультрасовременного Airbus A380 размах крыла «всего» 80 м.
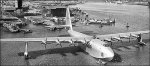
Изготовленная из фанеры гигантская летающая лодка Hughes H-4 Hercules. США, 1947 год
В начале XX века конструкторы и инженеры экспериментировали с фанерой и как с материалом для производства автомобилей. Из прочной, легкой и эластичной фанеры изготавливали части кузовов автомобилей, колясок и фургонов. На использование фанеры в автомобилестроении оказали влияние разработки в технологии производства самолетов и лодок, ряд компаний работали с фанерой в нескольких областях.
Изумительный по красоте гоночный автомобиль Hispano Suiza H6C Tulipwood с открытым кузовом сигарообразной формы, мотором объемом 7982 см3 и мощностью 200 л. с. был выпущен в 1924 году. Кузов, изготовленный по авиационной технологии, с оклейкой каркаса 3-миллиметровой авиационной фанерой произвела французская авиастроительная компания Nieuport, известная своими боевыми истребителями времен Первой мировой войны.
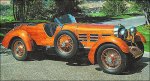
Гоночный автомобиль Hispano Suiza H6C Tulipwood с кузовом из авиационной фанеры. Франция, 1924 год
Особенно часто фанера применялась при производстве недорогих автомобилей. Немецкая компания DKW использовала формованную и плоскую фанеру для изготовления кузовов семейных автомобилей. В борьбе с предубеждением о ненадежности фанеры по сравнению с металлом в DKW продемонстрировали прочность фанеры, опубликовав рекламные фотоснимки работников фабрики, которые стояли на крыше одного из серийных автомобилей. После Второй мировой войны много подобных автомобилей попало в СССР, и отечественные острословы шутливо расшифровывали аббревиатуру DKW «Дерево, клей, вода».
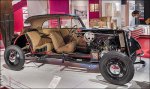
Разрез автомобиля марки DKW (модель F7) с кузовом из фанеры. Германия, 1938 год
После войны аналог модели F7 под маркой IFA выпускался в ГДР, пока ее не сменил знаменитый Trabant.
У используемых в те времена для склеивания фанеры клеев животного и растительного происхождения, таких как костный и рыбий, казеин и альбумин, водостойкость была ограниченной. Многочисленные исследования для разработки рецептуры клеев, устойчивых к воде, не давали результата, поэтому требовалось защищать фанеру лаком, наносимым в несколько слоев, иногда даже пять и более. Каждый слой лака необходимо было высушить, что сильно сказывалось на производительности и делало невозможным конвейерное производство. К тому же лаки того времени не обладали высокой атмосферостойкостью. Под действием погодных условий рано или поздно слои лака начинали шелушиться и растрескиваться. В результате фанера, из которой изготавливались детали кузова, под действием воды начинала расслаиваться, что заставило автомобилестроителей отказаться от фанеры в пользу штампованного металла.
Этот отказ стал сильным ударом для фанерной промышленности того времени и сигналом о том, что в производстве фанеры назрела фундаментальная проблема. Отсутствие водостойкого клея, который обеспечивал бы фанере высокую атмосферостойкость, постепенно подорвало доверие к ней и привело к банкротству многих производителей фанеры во время Великой депрессии в США 1929–1933 годов.
Настоящий технологический прорыв в производстве фанеры произошел в 1934 году. Американский инженер-химик из Harbor Plywood Corporation Джеймс Невин предложил для склеивания фанеры использовать водорастворимые альдегидные смолы. Разработанный им водостойкий клей позволил значительно расширить области применения фанеры, сделав ее абсолютно устойчивой к внешним атмосферным воздействиям. Интересно, что продолжались и попытки сделать водостойкие клеи на природной основе, например из рыбной муки, – сырье для подобных клеев производилось в больших объемах, а синтез фенолформальдегидных и других альдегидных смол был довольно новой технологией.
Прогресс в технологии производства фанеры, связанный с изобретением водостойких клеев, был настолько очевидным, что фанеру, изготовленную с использованием этих клеев, стали выпускать в США под отдельной торговой маркой Weldwood. Как следует из рекламных буклетов тех лет, фанера Weldwood годилась для производства сайдинга, рекламных щитов и дорожных знаков, сельскохозяйственных зданий, кузовов грузовиков, прицепов, фасадов магазинов, панелей для подвальных помещений, строительства лодок – словом, во всех областях, где до этого обычная фанера применялась ограниченно.
Изобретение Джеймса Невина дало мощный толчок использованию фанеры в судостроении. Если до появления водостойких клеев из нее в ограниченных количествах изготавливались небольшие каноэ и прогулочные лодки, то с появлением новой технологии фанеру стали применять для производства спасательных шлюпок, катеров, яхт, гоночных лодок и даже боевых судов – десантных, патрульных и торпедных катеров.
Одним из ярких примеров использования фанеры в малоразмерном судостроении были каноэ, которые в 1920-х годах изготавливала американская фирма Haskell. Каноэ были сделаны путем наборки и горячего прессования фанеры в фигурной пресс-форме с использованием альбуминового клея, который был разработан владельцем фирмы Генри Л. Хаскеллом. Каноэ были невероятно легкими – до 27 кг (60 фунтов), очень прочными и долговечными. На рекламном фото видно, что каноэ выдерживает вес семи взрослых мужчин, стоящих на нем. Позже компания Haskell использовала свой опыт работы с фигурным прессованием фанеры в пресс-формах с водостойкими клеями в производстве фанерных самолетов и транспортных средств.
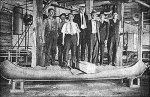
Каноэ, изготовленное из фанеры в компании Haskell Boat Company. США, 1917 год
После вступления во Вторую мировую войну в США возник острый дефицит металлов, особенно алюминия, вызванный повышенным спросом судостроителей и производителей самолетов. Армии и флоту потребовались конструкции боевой техники и учебного оборудования, которые могли быть изготовлены из фанеры. Инвестиции в заводы по выпуску Weldwood сразу начали расти. Фанера стала стратегически важным материалом, почти весь производимый объем уходил на нужды промышленности, поставленной на военные рельсы.
В громадных объемах из фанеры строились суда, активно используемые американцами во время десантных операций на Тихом океане. Во время высадки в Нормандии союзные войска переправлялись через Ла-Манш на судах, построенных в США и Великобритании из фанеры. Только компанией Higgins Boat было построено около 20 тыс. катеров LCVP длиной 36 футов и вместимостью 36 человек.
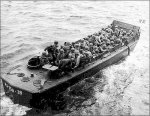
Десантный катер LCPV фирмы Higgins Boat, построенный из фанеры. США, 1943–1945 годы
Кстати, на одном из построенных из фанеры в годы Второй мировой войны патрульных торпедных катеров PT-109 служил будущий президент Соединенных Штатов Джон Ф. Кеннеди.
В СССР также в больших количествах выпускались аналогичные суда. У одного из серийных образцов торпедного катера проекта 183-А наружная обшивка была изготовлена из арктилита. Этот материал изготавливался из слоев березового шпона, чередующихся со слоями ткани типа миткаля и сеткой из тонкой стальной проволоки. Слои пропитывались или покрывались спиртовым раствором фенолформальдегидной смолы и после просушивания прессовались при высокой температуре. Арктилит хотя и обладал высокой прочностью, большого распространения не получил.
В 1930–1950-х годах фанера широко использовалась в производстве пассажирских и грузовых вагонов, рефрижераторов. Одной только фирмой Pacific Car and Foundry Company за четыре месяца 1941 года было выпущено более 1 тыс. рефрижераторов для перевозки фруктов. Каждые 40 минут за ворота завода выходил новенький рефрижератор, на изготовление которого уходило около 280 м2 фанеры. Использование фанеры позволило значительно упростить сборку, исключив из конструкции дефицитный металл.
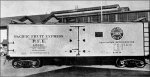
Рефрижератор для фруктов производства компании Pacific Car and Foundry Company. США, 1941 год
В США в 1940 годах была разработана и широко применялась фанера, облицованная с одной или двух сторон нержавеющей сталью и получившая товарное название Armorply. Толщина фанеры была 1/4–3/4 дюйма (от 6,5 до 20 мм), толщина стали – 0,0156 дюйма (0,4 мм). Перед облицовыванием фанера пропитывалась антипиренами.
Armorply использовалась для изготовления панелей корпуса легендарного в США скоростного дизель-электропоезда Zephyr, названного «Марк Твен».
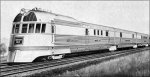
Дизель-электропоезд Zephyr с панелями корпуса из материала Armorply. США, 1935 год
В производстве упаковки фанеру начали использовать в начале XX века, чему невольно поспособствовал Эрнест Шеклтон. Знаменитый исследователь Антарктики заказал более 2500 фанерных ящиков для хранения и перевозки провианта и приборов. Шеклтон очень тщательно относился к подготовке экспедиции, и фанера была выбрана им из-за ее прочности и легкости. После экспедиции уцелевшие фанерные ящики использовались для изготовления мебели и даже в качестве переплета книги «Аврора Австралис», написанной Шеклтоном об экспедиции.
Из фанеры изготавливали ящики для оборудования, фруктов, инструмента, чемоданы, корпуса радиоприемников, швейных машинок и т. д.
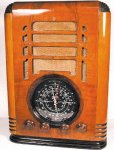
Изделия из фанеры – корпус радиоаппаратуры, радиоприемник ZENITH S-127, США, 1936 год
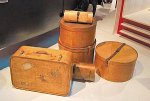
Изделия из фанеры – коробки, чемоданы
С распространением стиля модернизм в 1920-х годах архитекторы и дизайнеры начали применять фанеру для изготовления изделий причудливо изогнутой формы. Фанера хорошо подходила для массового производства, а используемая технология символизировала новый век технического прогресса.
В тот период появились изделия, которые и в наше время восхищают изяществом форм, простотой и гениальностью технических и дизайнерских решений.
Вот, например кресло, спроектированное финским архитектором Алваром Аалто. Тонкое гнутое сиденье подвешено между двумя узкими замкнутыми рамами и словно парит в воздухе. Мебель, созданная Аалто, экспортировалась в Великобританию и США, где это революционное дизайнерское решение использования фанеры оказало значительное влияние на других дизайнеров.

Кресло, спроектированное Алваром Аалто. Финляндия, 1932 год
Возможности фанеры наглядно продемонстрировали американские дизайнеры Чарльз и Рэй Эймсы, экспериментировавшие с фанерой во время Второй мировой войны при разработке методов формования сложных изогнутых форм.
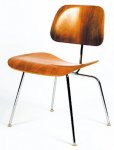
Изделия из фанеры – знаменитый стул Рэя Эймса. США, 1950 год
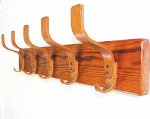
Изделия из фанеры – вешалка Бруно Пауля. Германия, 1930 год
Спроектированный ими стул с трехмерным формованным сиденьем был одним из самых известных стульев второй половины XX века. Стул был скопирован, и миллионы экземпляров появились по всему миру. Выдающийся английский промышленный дизайнер Робин Дей сказал о том времени расцвета дизайнерской мысли: «У каждого дизайнера, которого я знал, была фотография стула Эймса, прикрепленная к чертежной доске».
Справедливости ради надо отметить, что замечательные дизайнеры Чарльз и Рэй Эймсы не были пионерами в использовании гнутоклееной фанеры. Еще в викторианскую эпоху гнутоклееная фанера применялась при изготовлении мебели. Тем не менее они были самыми влиятельными дизайнерами мебели и сумели раскрыть всю красоту природного материала – древесины, придав ей причудливые и вместе с тем лаконичные формы. После их успеха появилась целая плеяда молодых дизайнеров, которые стали использовать фанеру в своих работах.
В строительстве фанера нашла широкое применение только с конца 1930 годов. Из нее изготавливали двери, перегородки, использовали для внутренней отделки жилых помещений. По-настоящему революционный прорыв в применении этого материала в домостроении произошел после появления атмосферостойкой фанеры. Из фанеры в США стали изготавливать не только стены, несущие конструкции и прочие строительные элементы, но и дома целиком.
Строительство подобных недорогих домов процветало в Соединенных Штатах в 1930-х годах, что объяснялось безработицей, невысокими доходами основной части населения и острой нехваткой дешевого жилья в Великую депрессию. Конструкции домов позволяли быстро изготавливать домокомплекты и легко собирать дома. Фанера отлично годилась для стандартных облегченных панельных систем, которые могли быть изготовлены на заводе и собраны на месте.
Лаборатория лесных товаров США (FPL) опубликовала схемы сборки экспериментального дома «Все из фанеры» с использованием стандартных фанерных панелей; его можно было бы производить на заводе, а затем быстро возводить на месте. В 1936 году был построен демонстрационный образец дома в г. Мэдисон, 12 тыс. посетителей шоу стояли в очереди, чтобы увидеть этот дом. Все детали были сделаны на заводе, и семь мужчин собрали дом всего за 21 час.
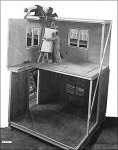
Использование фанеры в домостроении – полномасштабный быстровозводимый дом, построенный в г. Мэдисон в 1936 году
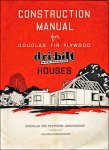
Использование фанеры в домостроении – разработанное FPL руководство по сборке домов из стандартных фанерных конструкций. США, 1937 год
В ходе умелой рекламной кампании были продемонстрированы все плюсы применения фанеры в строительной отрасли. За довольно короткое время было построено более 1 млн недорогих домов подобного типа, стоимостью от $2 тыс. до $7 тыс. Для сравнения: простенький автомобиль «форд» можно было купить в то время за $800, а престижный «кадиллак» – за $3–3,5 тысячи.
В домостроении фанера использовалась не только в качестве строительного материала. Архитекторы и дизайнеры того времени с ее помощью создавали удивительные по красоте интерьеры и фасады зданий.
Производство фанеры в дореволюционной России и в СССР до начала 1940-х годов
Историю создания фанерной промышленности дореволюционной России обычно представляют следующим образом.
В 1819 году профессор Фишер придумал метод получения облицовочной фанеры с помощью лущения. На изобретенном Фишером станке, который был известен еще как фанерный рубанок, можно было срезать ленту шпона с вращающегося бревна. Нож станка располагался по касательной к годичным кольцам древесины.
Фанера в том виде, в котором мы ее привыкли видеть сейчас, появилась в России позднее, примерно в середине XIX века. В 1881 году изобретатель и конструктор О. С. Костович разработал технологию производства трех- и многослойной фанеры, которую назвал арборитом, и конструкции машин для лущения шпона и склейки листов «клеем-цементом», изобретенным им же.
В 1880-х годах О. С. Костович оборудовал небольшую фабрику «Арборит» под Петербургом. Основной продукцией этого предприятия, на котором трудились всего 40 рабочих, были самые разные изделия из арборита: бочки для вина и керосина, ящики, сундуки, чемоданы, строительные детали и даже фанерные разборные домики. В опытном порядке в небольших количествах изготовлялись изделия из фанерных труб: лестницы, рангоуты парусных судов и т. д.
В 1906 году г-н Костович запатентовал технологию производства арборита в США.
В 1877 году столяр Александр Лютер и купец Маркел Макаров в 1885 году впервые в России наладили выпуск мебели из фанеры, которая пользовалась спросом не только в России, но и за ее пределами. В 1890 году эта мебель была удостоена золотой медали на Международной выставке в Мадриде, а через шесть лет на Нижегородской ярмарке мебель фабрики Лютера была удостоена большой золотой медали. После того как был запатентован изобретенный химиком фирмы О. Паулсеном водостойкий клей, продукция, выпускавшаяся этой фабрикой, неизменно пользовалась высоким спросом на российском и международном рынке.
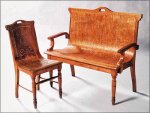
Мебель фабрики А. М. Лютера. Сиденье и спинки из цельного листа гнутоклееной фанеры. Россия, 1890 год
Первые заводы по производству клееной листовой фанеры были построены в 1894 году в Петербурге, а в 1896 году – вблизи Казани (Зеленодольский завод). С того времени производство клееной фанеры стало быстро развиваться, и к началу войны 1914 года в России насчитывалось 48 заводов, производивших 258,5 тыс. м3 фанеры в год.
Это были небольшие заводы, изготавливающие фанеру так называемым сырым способом клейки. Никакой механизации на них не было и в помине. Используемое оборудование даже для тех лет было крайне примитивным. У лущильных станков была ручная подача суппорта, прессы оснащались ручным гидравлическим насосом. Кряжи распиливали ручной пилой на чураки, которые рабочие переносили к станку на плечах. Клей на листы шпона наносился кистью или щеткой, а листы готовой фанеры обрезались ручной ножовкой.
После Гражданской войны в стране осталось только 28 фанерных предприятий, причем большая часть их была разрушена, 16 частично действовавших заводов вырабатывали всего 21,5 тыс. м3 фанеры в год. В 1922 году фанерные заводы, бездействовавшие до этого, были переданы Фанерному тресту, организованному Высшим Советом народного хозяйства. С того момента и началось восстановление, вернее, создание советской фанерной промышленности. С 1922 года по 1928 год были восстановлены и пущены почти все фанерные заводы, работавшие до революции.
Одновременно с борьбой за увеличение выпуска продукции была проделана значительная работа по повышению качества фанеры; в те годы начался перевод заводов на новый способ – сухую склейку; было положено начало производству специальной фанеры для авиастроения, а также сделаны первые попытки выпуска фасонной фанеры.
К концу второй пятилетки число фанерных заводов выросло до тридцати шести, выпуск фанеры был доведен до 672,3 тыс. м3. За годы второй пятилетки завод «Пролетарская свобода» освоил выпуск большинства видов фанерного оборудования, что можно считать крупным достижением советской промышленности. В СССР появились свои лущильные станки высокого качества, приводные ножницы, кромкофуговальные, ребросклеивающие, обрезные и прирезные станки, дробилки для отходов, дыхательные прессы, роликовые сушилки. Фанерная промышленность была избавлена от импортозависимости.
Большой вклад в становление производства фанеры внесла созданная в то время центральная лаборатория Фанеротреста (позднее Центральный научно-исследовательский институт фанеры – ЦНИИФ, единственный в Европе НИИ фанерной промышленности). Сотрудниками этого учреждения была разработана технологическая документация по всем основным процессам производства фанеры. Наконец, была создана широкая сеть оснащенных заводских лабораторий, что позволило наладить систематический контроль технологии производства и проводить анализ клеевых материалов и качества фанеры.
Изучая историю фанеры, невольно задумываешься: есть ли будущее у этого материала? Или синтетические пластики, ДСтП, плиты OSB и MDF в конце концов вытеснят фанеру из нашей жизни? Думаю, что в обозримом будущем этого не произойдет. Ведь фанера – это та же древесина, лишь слегка усовершенствованная человеком. С ее притягательной живой красотой и внутренней теплотой не способен поспорить ни один самый современный синтетический материал.
Фанера была известна людям еще на заре цивилизации. Самый старый, полуистлевший кусок фанеры, относящийся примерно к 2600 г. до н. э., найден в Египте в одной из усыпальниц члена семьи фараона третьей династии Джосера. Алебастровый саркофаг был обшит изнутри шестислойной фанерой. Слои древесины толщиной 4 мм скреплялись деревянными гвоздиками и чрезвычайно плотно прилегали друг к другу. Как и в современной фанере, расположение слоев было взаимно перпендикулярным!
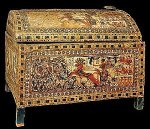
Ларец из гробницы Тутанхамона. Египет, 1332 год до н. э
Судя по найденным в Египте артефактам, начиная с 1750 года до н. э. технология фанерования получила широкое распространение. В Египте того времени не было ни больших лесов, ни высоких деревьев. Местные акация, можжевельник, платан и деревья других пород с древесиной в основном низкого качества могли распиливаться только на небольшие доски. Ценимое египтянами черное дерево ввозились из Восточной Африки, а кедр и сосна – из Ливана. Стоимость древесины была очень высокой, именно это в конечном счете и заставило древних мастеров использовать технологию фанерования. Производство было очень трудоемким – слои фанеры изготавливались вручную путем продольной распиловки стволов тонкими (0,5–1,5 мм толщиной) медными пилами с треугольными зубьями. В найденных произведениях искусства египетских краснодеревщиков толщина слоев древесины составляла менее 3 мм, и они уже были соединены клеем. Этот клей изготавливался из содержащих желатин продуктов животного происхождения: костей, кож, сухожилий и хрящей.
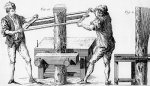
Изготовление шпона пилением. Европа, начало XVII века
Впоследствии метод фанерования стали использовать в Древнем Риме и Греции. Известно, что и древние китайцы применяли подобную технику при производстве мебели. В этих странах так же, как и в Египте, постоянно ощущался дефицит древесины ценных пород. Она завозилась издалека и была очень дорогой.
Значительно позже технологию производства фанеры освоили в Европе. Мебель, изготовленная французскими мастерами в XV–XVI веках для украшения королевских и дворянских замков, очень часто фанеровалась тонкими дощечками из ценных и редких пород красного и черного дерева. Подобная мебель стоила немало, но все-таки была дешевле изготовленной из цельной древесины, поэтому пользовалась большим спросом и была доступна среднему классу нарождающейся буржуазии. Со временем появилась необходимость в совершенствовании технологии и оборудования производства фанеры, так как вплоть до конца XVIII века шпон изготавливали вручную, а потому цена фанеры была высокой, а ее качество оставляло желать лучшего.
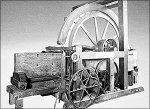
Станок братьев Мундинг для изготовления шпона пилением. Австрия, 1800 год
Попытки механизировать процесс производства шпона предпринимались еще в начале XVIII века. Первый английский патент, относящийся к производству шпона, был предоставлен в 1635 году Саре Джером и Уильяму Уэббу, за «двигатель для резки древесины в тонкие чешуйки» для изготовления бандажей, ножен для мечей и т. п.
Однако, несмотря на то что производство фанерованной мебели значительно выросло и требовалось все больше качественного шпона, период с 1700 по 1830 год был временем расцвета ручного пиления и использования ручного резака для получения шпона.
Растущий спрос на декоративную мебель состоятельных аристократов, среднего класса и священнослужителей крупных городов в XIX веке привел к изменениям в технике для изготовления шпона.
В Вене того времени было много богачей, которые хотели обставить свои дома мебелью, изготовленной из шпона ценных пород древесины, и австрийцы Алоис и Мартин Мундинг еще в 1800 году стали использовать машину для резки шпона. Этот деревообрабатывающий «бегемот» имел длину 6 м и высоту более 3 м. Двое рабочих управляли им с помощью педалей. При изготовлении шпона на таком станке древесная стружка и опилки составляли четверть или даже половину первоначального объема распиливаемой заготовки.
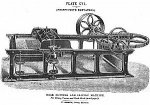
Горизонтальный строгальный станок Арбея. Франция, 1875 год
В 1806 году выдающийся английский инженер французского происхождения Марк Исамбард Брунель получил британский патент на строгальный станок с ручным приводом. Этот станок стал прообразом современных строгальных станков с горизонтально движущимся ножом. Станок хорошо резал прямослойную древесину красного дерева, но при строгании плотного палисандра потерпел полное фиаско. В дальнейшем Брунель отказался от принципа изготовления шпона строганием, сосредоточившись на создании станка для раскроя древесины с помощью циркулярной пилы сегментного типа. Разработанный им станок, оснащенный паровой машиной мощностью 16 л. с., позволял распиливать доски из красного дерева и палисандра на шпон толщиной всего 1/16 дюйма (1,6 мм). Станки Брунеля успешно использовались на заводах по производству шпона по всей Великобритании. На некоторых заводах было установлено больше десятка станков с пилами от 7 до 17 футов в диаметре! Производительность подобного оборудования была невысокой, так как скорость подачи не превышала четверти фута в секунду.
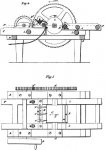
Лущильный станок, разработанный Генри Хамфри. США, 1842 год
К идее изготовления шпона способом горизонтального строгания в 1875 году вернулся французский изобретатель Арбей. Разработанные им станки позволяли изготавливать шпон толщиной 1/100 дюйма, качество поверхности было таким высоким, что шлифование не требовалось.
Однако настоящий прорыв в технологии производства фанеры был сделан только после изобретения технологии резания вращающегося бревна (чурака) ножом, движущимся поступательно к оси вращения. Общепризнанный приоритет технологии роторной резки шпона или лущения – за российскими инженерами начала XIX века. В отчете, опубликованном в Великобритании в 1817 году, было сказано, что российский изобретатель в Санкт-Петербурге сделал станок, который производит «листы фанеры около ста футов в длину и четыре, пять или даже больше в ширину».
Похожую машину в Англии в 1818 году запатентовал Генри Фаверир. О практическом применении машины Фаверира ничего не известно. Через некоторое время подобный станок был разработан в США и как «улучшенный роторный резак шпона, приводимый в движение паром», использовался промышленником Ричардсоном в Филадельфии в 1825 году.
Интересно, что конструкция и узлы современных лущильных станков по сути идентичны конструкции и узлам станков, разработанных еще в середине XIX века. Например, на рисунке к патенту, выданному в 1842 году Генри Хамфри, можно видеть подвижный суппорт с закрепленным ножом, обжимной и поддерживающий ролики, подрезные ножи и т. д.
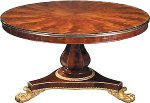
Стол из фанеры, облицованной шпоном махагони. Франция, XIX век
В 1843 году в энциклопедической статье (Penny Cyclopedia, 1843) резка шпона описывалась так: «В России с помощью строгальной машины изготавливают шпон, который настолько тонок, что может использоваться для книжных переплетов, причем лента шпона сто футов в длину была нарезана этой машиной в течение трех минут».
Лондонский журнал Mechanic’s magazine в статье, опубликованной в 1848 году, отмечал значительное преимущество роторной резки по производительности перед другими способами изготовления шпона. В статье описывалась машина, которая могла нарезать рулон кленового шпона длиной 300 футов и шириной 3 фута из бревна диаметром 20 дюймов.
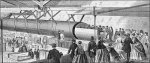
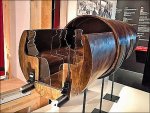
Прототип подвесной железной дороги Альфреда Эли Бича, изготовленный из фанеры. США, 1867 год вверху – общий вид; снизу – вагон, вмещающий 10 пассажиров
Однако технология роторной резки шпона получила признание не сразу. Автор словаря производств Джордж Додд в 1860 году писал: «Хотя при изготовлении шпона в Англии пилами Брунеля расходуется больше древесины, этот способ дает более качественный шпон, чем роторный метод, получивший распространение на континенте».
Повышению качества шпона роторной резки способствовало внедрение предварительного замачивания бревен для смягчения древесины. Вероятным новатором был француз Гаранд, придумавший этот метод в 1860 году. Вскоре замачивание, в том числе и в горячей воде, стало применяться повсеместно, хотя и влияло на цвет шпона.
Споры о качества шпона, получаемого различными способами, продолжались во второй половине XIX века. Известный английский инженер Чарльз Хольцзаффель предположил, что шпон, полученный роторной резкой, будет скручиваться и расщепляться. С другой стороны, корреспондент издания Universal Decorator отмечал, что шпон, полученный лущением, вызовет настоящий бум производства мебели.
Считается, что первый патент на фанеру в том виде, в каком она выпускается сегодня, был выдан Джону К. Майо в 1865 году. Однако сделанное им изобретение кануло в Лету, так как Майо не пытался получить коммерческую выгоду от его использования.
Машинное производство шпона позволило значительно снизить стоимость фанеры, многократно повысить качество материала, которое существенно превосходило качество фанеры ручного изготовления и выпускать мебель по доступным ценам.
Хотя в те времена фанера использовалась преимущественно для изготовления мебели, были и попытки применять ее в весьма необычных проектах. Так, удивительно смелая даже по нынешним временам идея построить в Нью-Йорке пневматический надземный метрополитен пришла в голову богатому бизнесмену и изобретателю Альфреду Эли Бичу, своего рода Илону Маску того времени. Он планировал протянуть подвесную дорогу по всему городу на столбчатых опорах либо прикреплять ее к стенам зданий. Прототип дороги длиной 107 футов в виде формованной фанерной трубы был продемонстрирован в 1867 году в большом выставочном зале американского института в Нью-Йорке. Установленные на обоих концах трубы гигантские вентиляторы создавали напор воздуха достаточный для того, чтобы посетители выставки могли ездить внутри трубы в цилиндрических вагончиках, также изготовленных из фанеры и вмещающих десять человек, туда и обратно.
Несмотря на очевидные достижения как в области оборудования и технологии производства, так и в применении, популярным строительным материалом фанера стала только в начале 1900-х годов, чему в немалой степени способствовала всемирная выставка 1905 года в американском Портленде. В этом городе был один из первых фанерных заводов США Portland Manufacturing. Владелец завода Густав Карлсон изготовил несколько образцов фанеры из местных хвойных пород, используя для нанесения клея малярные кисти, а для прессования автомобильные домкраты. Новый материал вызвал большой интерес у производителей дверей, легковых автомобилей и грузовиков, строителей. Заказы потекли рекой. К 1907 году компания установила станок для нанесения клея и ручной пресс. Производство выросло до 420 листов фанеры в день.
Наиболее технологически значимой сферой применения фанеры с 1910 по 1945 год стало самолетостроение. Прочность и легкость материала позволили проектировать и изготавливать принципиально новые, прогрессивные для того времени конструкции самолетов.
Еще в начале 1910 годов новаторские эксперименты с формованной фанерой позволили построить первый закрытый, обтекаемый фюзеляж самолета – монокок (от фр. мonocoque, означает «единая оболочка»), ставший тогда стандартом в конструировании самолетов.
Фюзеляж, сделанный по принципу монокока, состоял из внешней оболочки, изготовленной из фанеры, форма которой удерживалась несколькими внутренними поперечными переборками. Революционный по тому времени монокок, конструкция которого была несущей, имел гладкую обтекаемую форму, отличался прочностью, жесткостью и легкостью. Французский инженер Луис Бекеро в 1911 году впервые использовал фанерную монококовую конструкцию в фюзеляже гоночного моноплана Deperdussion.
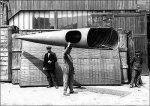
Фюзеляж истребителя SPAD-Deperdussin представлял собой конструкцию в виде монокока, выклеенного из фанеры, и настолько легкую, что его мог спокойно переносить один рабочий. Франция, 1913 год
Позже конструкцию фюзеляжа в виде монокока из фанеры использовали авиастроители при создании самых известных и скоростных истребителей Первой мировой войны Bleriot-SPAD, Albatross D-III.
В 1930-е годы в СССР, испытывавшем острый недостаток алюминия, фанера также широко использовалась в авиастроении. Отечественные инженеры создавали из фанеры самолеты оригинальных, новаторских конструкций.
В 1928 году в Ленинградском институте инженеров путей сообщения, в студенческом самолетном кружке, возглавляемом В. Ф. Рентелем, возникла мысль построить опытный самолет из фанеры. Широкое применение фанеры в конструкции с обусловило второе название самолета: «Фанера-2». Построенные небольшой серией эти самолеты успешно эксплуатировались на местных линиях Аэрофлота, в Арктике и на Дальнем Востоке.
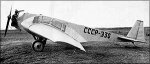
Самолет «Фанера-2», изготовленный почти целиком из фанеры. СССР, 1933 год
Фанера широко использовалась при создании боевых самолетов времен Второй мировой войны. У британского de Havilland Mosquito (DH-98), одного из самых известных самолетов того времени, был формованный фанерный фюзеляж-монокок – легкий и обтекаемый. Поэтому даже с довольно маломощными моторами он был настолько быстрым, что летал без оборонительного вооружения. Немецкие истребители ПВО просто не могли его догнать.
Интересно, что министерство авиации Великобритании хотело, чтобы на вооружение поступил самолет, изготовленный из металла, и первоначально отвергло проект. Однако конструкторы фирмы de Havilland Aircraft Company доказали, что можно создать технологичный и дешевый самолет из фанеры, используя неквалифицированный труд работников мебельных и деревообрабатывающих заводов в Великобритании, Австралии и Канаде.
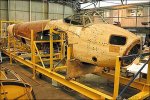
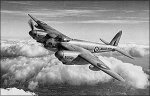
Самолет de Havilland Mosquito (DH-98). Великобритания: вверху – фюзеляж-монокок из фанеры на стапеле в процессе реставрации; внизу – самолет в полете
Самым ярким примером использования фанеры в самолетостроении является транспортная летающая лодка Hughes H-4 Hercules, разработанная американской фирмой Hughes Aircraft под руководством Говарда Хьюза в 1947 году. Этот гигантский 136-тонный самолет первоначально получил прозвище Spruce Goose (дословно «Еловый гусь»). Несмотря на «хвойное» название, самолет был почти полностью построен из выклеенной по шаблону березовой фанеры. H-4 – самая большая из когда-либо построенных летающих лодок, размах ее крыла – 98 м оставался рекордным для самолетов до 2017 года. Для сравнения: у ультрасовременного Airbus A380 размах крыла «всего» 80 м.
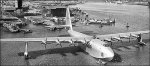
Изготовленная из фанеры гигантская летающая лодка Hughes H-4 Hercules. США, 1947 год
В начале XX века конструкторы и инженеры экспериментировали с фанерой и как с материалом для производства автомобилей. Из прочной, легкой и эластичной фанеры изготавливали части кузовов автомобилей, колясок и фургонов. На использование фанеры в автомобилестроении оказали влияние разработки в технологии производства самолетов и лодок, ряд компаний работали с фанерой в нескольких областях.
Изумительный по красоте гоночный автомобиль Hispano Suiza H6C Tulipwood с открытым кузовом сигарообразной формы, мотором объемом 7982 см3 и мощностью 200 л. с. был выпущен в 1924 году. Кузов, изготовленный по авиационной технологии, с оклейкой каркаса 3-миллиметровой авиационной фанерой произвела французская авиастроительная компания Nieuport, известная своими боевыми истребителями времен Первой мировой войны.
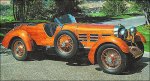
Гоночный автомобиль Hispano Suiza H6C Tulipwood с кузовом из авиационной фанеры. Франция, 1924 год
Особенно часто фанера применялась при производстве недорогих автомобилей. Немецкая компания DKW использовала формованную и плоскую фанеру для изготовления кузовов семейных автомобилей. В борьбе с предубеждением о ненадежности фанеры по сравнению с металлом в DKW продемонстрировали прочность фанеры, опубликовав рекламные фотоснимки работников фабрики, которые стояли на крыше одного из серийных автомобилей. После Второй мировой войны много подобных автомобилей попало в СССР, и отечественные острословы шутливо расшифровывали аббревиатуру DKW «Дерево, клей, вода».
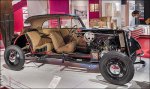
Разрез автомобиля марки DKW (модель F7) с кузовом из фанеры. Германия, 1938 год
После войны аналог модели F7 под маркой IFA выпускался в ГДР, пока ее не сменил знаменитый Trabant.
У используемых в те времена для склеивания фанеры клеев животного и растительного происхождения, таких как костный и рыбий, казеин и альбумин, водостойкость была ограниченной. Многочисленные исследования для разработки рецептуры клеев, устойчивых к воде, не давали результата, поэтому требовалось защищать фанеру лаком, наносимым в несколько слоев, иногда даже пять и более. Каждый слой лака необходимо было высушить, что сильно сказывалось на производительности и делало невозможным конвейерное производство. К тому же лаки того времени не обладали высокой атмосферостойкостью. Под действием погодных условий рано или поздно слои лака начинали шелушиться и растрескиваться. В результате фанера, из которой изготавливались детали кузова, под действием воды начинала расслаиваться, что заставило автомобилестроителей отказаться от фанеры в пользу штампованного металла.
Этот отказ стал сильным ударом для фанерной промышленности того времени и сигналом о том, что в производстве фанеры назрела фундаментальная проблема. Отсутствие водостойкого клея, который обеспечивал бы фанере высокую атмосферостойкость, постепенно подорвало доверие к ней и привело к банкротству многих производителей фанеры во время Великой депрессии в США 1929–1933 годов.
Настоящий технологический прорыв в производстве фанеры произошел в 1934 году. Американский инженер-химик из Harbor Plywood Corporation Джеймс Невин предложил для склеивания фанеры использовать водорастворимые альдегидные смолы. Разработанный им водостойкий клей позволил значительно расширить области применения фанеры, сделав ее абсолютно устойчивой к внешним атмосферным воздействиям. Интересно, что продолжались и попытки сделать водостойкие клеи на природной основе, например из рыбной муки, – сырье для подобных клеев производилось в больших объемах, а синтез фенолформальдегидных и других альдегидных смол был довольно новой технологией.
Прогресс в технологии производства фанеры, связанный с изобретением водостойких клеев, был настолько очевидным, что фанеру, изготовленную с использованием этих клеев, стали выпускать в США под отдельной торговой маркой Weldwood. Как следует из рекламных буклетов тех лет, фанера Weldwood годилась для производства сайдинга, рекламных щитов и дорожных знаков, сельскохозяйственных зданий, кузовов грузовиков, прицепов, фасадов магазинов, панелей для подвальных помещений, строительства лодок – словом, во всех областях, где до этого обычная фанера применялась ограниченно.
Изобретение Джеймса Невина дало мощный толчок использованию фанеры в судостроении. Если до появления водостойких клеев из нее в ограниченных количествах изготавливались небольшие каноэ и прогулочные лодки, то с появлением новой технологии фанеру стали применять для производства спасательных шлюпок, катеров, яхт, гоночных лодок и даже боевых судов – десантных, патрульных и торпедных катеров.
Одним из ярких примеров использования фанеры в малоразмерном судостроении были каноэ, которые в 1920-х годах изготавливала американская фирма Haskell. Каноэ были сделаны путем наборки и горячего прессования фанеры в фигурной пресс-форме с использованием альбуминового клея, который был разработан владельцем фирмы Генри Л. Хаскеллом. Каноэ были невероятно легкими – до 27 кг (60 фунтов), очень прочными и долговечными. На рекламном фото видно, что каноэ выдерживает вес семи взрослых мужчин, стоящих на нем. Позже компания Haskell использовала свой опыт работы с фигурным прессованием фанеры в пресс-формах с водостойкими клеями в производстве фанерных самолетов и транспортных средств.
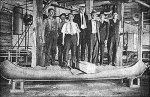
Каноэ, изготовленное из фанеры в компании Haskell Boat Company. США, 1917 год
После вступления во Вторую мировую войну в США возник острый дефицит металлов, особенно алюминия, вызванный повышенным спросом судостроителей и производителей самолетов. Армии и флоту потребовались конструкции боевой техники и учебного оборудования, которые могли быть изготовлены из фанеры. Инвестиции в заводы по выпуску Weldwood сразу начали расти. Фанера стала стратегически важным материалом, почти весь производимый объем уходил на нужды промышленности, поставленной на военные рельсы.
В громадных объемах из фанеры строились суда, активно используемые американцами во время десантных операций на Тихом океане. Во время высадки в Нормандии союзные войска переправлялись через Ла-Манш на судах, построенных в США и Великобритании из фанеры. Только компанией Higgins Boat было построено около 20 тыс. катеров LCVP длиной 36 футов и вместимостью 36 человек.
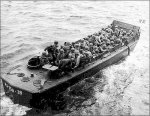
Десантный катер LCPV фирмы Higgins Boat, построенный из фанеры. США, 1943–1945 годы
Кстати, на одном из построенных из фанеры в годы Второй мировой войны патрульных торпедных катеров PT-109 служил будущий президент Соединенных Штатов Джон Ф. Кеннеди.
В СССР также в больших количествах выпускались аналогичные суда. У одного из серийных образцов торпедного катера проекта 183-А наружная обшивка была изготовлена из арктилита. Этот материал изготавливался из слоев березового шпона, чередующихся со слоями ткани типа миткаля и сеткой из тонкой стальной проволоки. Слои пропитывались или покрывались спиртовым раствором фенолформальдегидной смолы и после просушивания прессовались при высокой температуре. Арктилит хотя и обладал высокой прочностью, большого распространения не получил.
В 1930–1950-х годах фанера широко использовалась в производстве пассажирских и грузовых вагонов, рефрижераторов. Одной только фирмой Pacific Car and Foundry Company за четыре месяца 1941 года было выпущено более 1 тыс. рефрижераторов для перевозки фруктов. Каждые 40 минут за ворота завода выходил новенький рефрижератор, на изготовление которого уходило около 280 м2 фанеры. Использование фанеры позволило значительно упростить сборку, исключив из конструкции дефицитный металл.
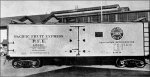
Рефрижератор для фруктов производства компании Pacific Car and Foundry Company. США, 1941 год
В США в 1940 годах была разработана и широко применялась фанера, облицованная с одной или двух сторон нержавеющей сталью и получившая товарное название Armorply. Толщина фанеры была 1/4–3/4 дюйма (от 6,5 до 20 мм), толщина стали – 0,0156 дюйма (0,4 мм). Перед облицовыванием фанера пропитывалась антипиренами.
Armorply использовалась для изготовления панелей корпуса легендарного в США скоростного дизель-электропоезда Zephyr, названного «Марк Твен».
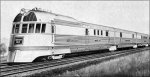
Дизель-электропоезд Zephyr с панелями корпуса из материала Armorply. США, 1935 год
В производстве упаковки фанеру начали использовать в начале XX века, чему невольно поспособствовал Эрнест Шеклтон. Знаменитый исследователь Антарктики заказал более 2500 фанерных ящиков для хранения и перевозки провианта и приборов. Шеклтон очень тщательно относился к подготовке экспедиции, и фанера была выбрана им из-за ее прочности и легкости. После экспедиции уцелевшие фанерные ящики использовались для изготовления мебели и даже в качестве переплета книги «Аврора Австралис», написанной Шеклтоном об экспедиции.
Из фанеры изготавливали ящики для оборудования, фруктов, инструмента, чемоданы, корпуса радиоприемников, швейных машинок и т. д.
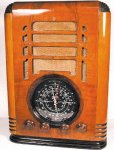
Изделия из фанеры – корпус радиоаппаратуры, радиоприемник ZENITH S-127, США, 1936 год
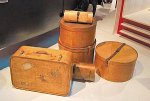
Изделия из фанеры – коробки, чемоданы
С распространением стиля модернизм в 1920-х годах архитекторы и дизайнеры начали применять фанеру для изготовления изделий причудливо изогнутой формы. Фанера хорошо подходила для массового производства, а используемая технология символизировала новый век технического прогресса.
В тот период появились изделия, которые и в наше время восхищают изяществом форм, простотой и гениальностью технических и дизайнерских решений.
Вот, например кресло, спроектированное финским архитектором Алваром Аалто. Тонкое гнутое сиденье подвешено между двумя узкими замкнутыми рамами и словно парит в воздухе. Мебель, созданная Аалто, экспортировалась в Великобританию и США, где это революционное дизайнерское решение использования фанеры оказало значительное влияние на других дизайнеров.

Кресло, спроектированное Алваром Аалто. Финляндия, 1932 год
Возможности фанеры наглядно продемонстрировали американские дизайнеры Чарльз и Рэй Эймсы, экспериментировавшие с фанерой во время Второй мировой войны при разработке методов формования сложных изогнутых форм.
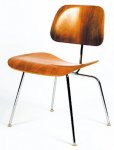
Изделия из фанеры – знаменитый стул Рэя Эймса. США, 1950 год
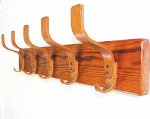
Изделия из фанеры – вешалка Бруно Пауля. Германия, 1930 год
Спроектированный ими стул с трехмерным формованным сиденьем был одним из самых известных стульев второй половины XX века. Стул был скопирован, и миллионы экземпляров появились по всему миру. Выдающийся английский промышленный дизайнер Робин Дей сказал о том времени расцвета дизайнерской мысли: «У каждого дизайнера, которого я знал, была фотография стула Эймса, прикрепленная к чертежной доске».
Справедливости ради надо отметить, что замечательные дизайнеры Чарльз и Рэй Эймсы не были пионерами в использовании гнутоклееной фанеры. Еще в викторианскую эпоху гнутоклееная фанера применялась при изготовлении мебели. Тем не менее они были самыми влиятельными дизайнерами мебели и сумели раскрыть всю красоту природного материала – древесины, придав ей причудливые и вместе с тем лаконичные формы. После их успеха появилась целая плеяда молодых дизайнеров, которые стали использовать фанеру в своих работах.
В строительстве фанера нашла широкое применение только с конца 1930 годов. Из нее изготавливали двери, перегородки, использовали для внутренней отделки жилых помещений. По-настоящему революционный прорыв в применении этого материала в домостроении произошел после появления атмосферостойкой фанеры. Из фанеры в США стали изготавливать не только стены, несущие конструкции и прочие строительные элементы, но и дома целиком.
Строительство подобных недорогих домов процветало в Соединенных Штатах в 1930-х годах, что объяснялось безработицей, невысокими доходами основной части населения и острой нехваткой дешевого жилья в Великую депрессию. Конструкции домов позволяли быстро изготавливать домокомплекты и легко собирать дома. Фанера отлично годилась для стандартных облегченных панельных систем, которые могли быть изготовлены на заводе и собраны на месте.
Лаборатория лесных товаров США (FPL) опубликовала схемы сборки экспериментального дома «Все из фанеры» с использованием стандартных фанерных панелей; его можно было бы производить на заводе, а затем быстро возводить на месте. В 1936 году был построен демонстрационный образец дома в г. Мэдисон, 12 тыс. посетителей шоу стояли в очереди, чтобы увидеть этот дом. Все детали были сделаны на заводе, и семь мужчин собрали дом всего за 21 час.
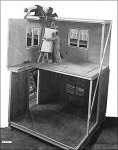
Использование фанеры в домостроении – полномасштабный быстровозводимый дом, построенный в г. Мэдисон в 1936 году
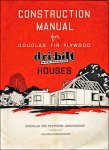
Использование фанеры в домостроении – разработанное FPL руководство по сборке домов из стандартных фанерных конструкций. США, 1937 год
В ходе умелой рекламной кампании были продемонстрированы все плюсы применения фанеры в строительной отрасли. За довольно короткое время было построено более 1 млн недорогих домов подобного типа, стоимостью от $2 тыс. до $7 тыс. Для сравнения: простенький автомобиль «форд» можно было купить в то время за $800, а престижный «кадиллак» – за $3–3,5 тысячи.
В домостроении фанера использовалась не только в качестве строительного материала. Архитекторы и дизайнеры того времени с ее помощью создавали удивительные по красоте интерьеры и фасады зданий.
Производство фанеры в дореволюционной России и в СССР до начала 1940-х годов
Историю создания фанерной промышленности дореволюционной России обычно представляют следующим образом.
В 1819 году профессор Фишер придумал метод получения облицовочной фанеры с помощью лущения. На изобретенном Фишером станке, который был известен еще как фанерный рубанок, можно было срезать ленту шпона с вращающегося бревна. Нож станка располагался по касательной к годичным кольцам древесины.
Фанера в том виде, в котором мы ее привыкли видеть сейчас, появилась в России позднее, примерно в середине XIX века. В 1881 году изобретатель и конструктор О. С. Костович разработал технологию производства трех- и многослойной фанеры, которую назвал арборитом, и конструкции машин для лущения шпона и склейки листов «клеем-цементом», изобретенным им же.
В 1880-х годах О. С. Костович оборудовал небольшую фабрику «Арборит» под Петербургом. Основной продукцией этого предприятия, на котором трудились всего 40 рабочих, были самые разные изделия из арборита: бочки для вина и керосина, ящики, сундуки, чемоданы, строительные детали и даже фанерные разборные домики. В опытном порядке в небольших количествах изготовлялись изделия из фанерных труб: лестницы, рангоуты парусных судов и т. д.
В 1906 году г-н Костович запатентовал технологию производства арборита в США.
В 1877 году столяр Александр Лютер и купец Маркел Макаров в 1885 году впервые в России наладили выпуск мебели из фанеры, которая пользовалась спросом не только в России, но и за ее пределами. В 1890 году эта мебель была удостоена золотой медали на Международной выставке в Мадриде, а через шесть лет на Нижегородской ярмарке мебель фабрики Лютера была удостоена большой золотой медали. После того как был запатентован изобретенный химиком фирмы О. Паулсеном водостойкий клей, продукция, выпускавшаяся этой фабрикой, неизменно пользовалась высоким спросом на российском и международном рынке.
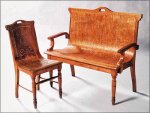
Мебель фабрики А. М. Лютера. Сиденье и спинки из цельного листа гнутоклееной фанеры. Россия, 1890 год
Первые заводы по производству клееной листовой фанеры были построены в 1894 году в Петербурге, а в 1896 году – вблизи Казани (Зеленодольский завод). С того времени производство клееной фанеры стало быстро развиваться, и к началу войны 1914 года в России насчитывалось 48 заводов, производивших 258,5 тыс. м3 фанеры в год.
Это были небольшие заводы, изготавливающие фанеру так называемым сырым способом клейки. Никакой механизации на них не было и в помине. Используемое оборудование даже для тех лет было крайне примитивным. У лущильных станков была ручная подача суппорта, прессы оснащались ручным гидравлическим насосом. Кряжи распиливали ручной пилой на чураки, которые рабочие переносили к станку на плечах. Клей на листы шпона наносился кистью или щеткой, а листы готовой фанеры обрезались ручной ножовкой.
После Гражданской войны в стране осталось только 28 фанерных предприятий, причем большая часть их была разрушена, 16 частично действовавших заводов вырабатывали всего 21,5 тыс. м3 фанеры в год. В 1922 году фанерные заводы, бездействовавшие до этого, были переданы Фанерному тресту, организованному Высшим Советом народного хозяйства. С того момента и началось восстановление, вернее, создание советской фанерной промышленности. С 1922 года по 1928 год были восстановлены и пущены почти все фанерные заводы, работавшие до революции.
Одновременно с борьбой за увеличение выпуска продукции была проделана значительная работа по повышению качества фанеры; в те годы начался перевод заводов на новый способ – сухую склейку; было положено начало производству специальной фанеры для авиастроения, а также сделаны первые попытки выпуска фасонной фанеры.
К концу второй пятилетки число фанерных заводов выросло до тридцати шести, выпуск фанеры был доведен до 672,3 тыс. м3. За годы второй пятилетки завод «Пролетарская свобода» освоил выпуск большинства видов фанерного оборудования, что можно считать крупным достижением советской промышленности. В СССР появились свои лущильные станки высокого качества, приводные ножницы, кромкофуговальные, ребросклеивающие, обрезные и прирезные станки, дробилки для отходов, дыхательные прессы, роликовые сушилки. Фанерная промышленность была избавлена от импортозависимости.
Большой вклад в становление производства фанеры внесла созданная в то время центральная лаборатория Фанеротреста (позднее Центральный научно-исследовательский институт фанеры – ЦНИИФ, единственный в Европе НИИ фанерной промышленности). Сотрудниками этого учреждения была разработана технологическая документация по всем основным процессам производства фанеры. Наконец, была создана широкая сеть оснащенных заводских лабораторий, что позволило наладить систематический контроль технологии производства и проводить анализ клеевых материалов и качества фанеры.
Изучая историю фанеры, невольно задумываешься: есть ли будущее у этого материала? Или синтетические пластики, ДСтП, плиты OSB и MDF в конце концов вытеснят фанеру из нашей жизни? Думаю, что в обозримом будущем этого не произойдет. Ведь фанера – это та же древесина, лишь слегка усовершенствованная человеком. С ее притягательной живой красотой и внутренней теплотой не способен поспорить ни один самый современный синтетический материал.
Александр ФИЛИППОВИЧ
Источник: lesprominform.ru