- Регистрация
- 22 Мар 2017
- Сообщения
- 153
- Реакции
- 183
- Баллы
- 43
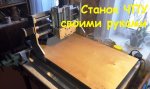
Собираю очередной портально–фрезерный станок с небольшим рабочим полем по дереву, пластику, композитам. Об этом повествование приведено под катом…
Скажу сразу — не у всех завалялось в гараже то, что у меня. Ввиду некоторых сторонних механических проектов, у меня скопился некий хлам, который впоследствии мог бы просто заржаветь, после чего, его только в чермет. К такому виду хлама я отнес полированные направляющие валы, немного обрезков дюралевых листов (хоть и не заржавеют, но занимают место). Еще у меня оказался в наличии шаговый двигатель и драйвер.
Помимо всего прочего, из основного осталось доукомплектовать мой имеющийся набор: ШВП, каретками для направляющих валов, двигателями, электроникой и шпинделем. В общем “самую малость”. И при наличии всего этого, не считая всяких мелочей в виде металлообработки и различных метиз, у меня получится станок с ЧПУ.
Прикинув ценник на недостающие комплектующие, и поняв, что осилю такую сумму без особых финансовых затруднений (особенно если покупать все не сразу, а по мере сборки), я все же решился на столь опрометчивый шаг и занялся проектированием будущего станка.
Исходя из длин направляющих и размеров обрезков дюрали (благо они были примерно все одного размера), начал с прорисовки основания.
Размеры:
Обрезки – длина 700мм, высота 70мм, толщина 6 мм.
Направляющие (4 штуки) – диаметр 25мм, длина 740мм.
От этих размеров и отталкивался в ходе построения всей конструкции. Соответственно длина перемещения портала вдоль основания получилась 600мм (X координата).
Ввиду того, что направляющих всего 4 штуки, а докупать их не планировалось, и к тому же у станка три оси перемещения, пришлось делить две направляющие на две более маленьких оси: Y и Z. Поделил так, что ширина рабочего поля по Y получилась 250мм, а по Z — 80мм.
Так как это не первый мой проект станка с чпу, то вместо привычного КОМПАС 3D я использовал SolidWorks. В нем были перерисованы все имеющиеся у меня в наличии и заказанные стандартные детали (двигатели, муфты, направляющие каретки, подшипниковые опоры, ШВП гайки, опоры направляющих), не требующие дополнительной обработки. Далее начал добавлять в проект направляющие, стал их связывать дюралевыми листами, в которых делал технологические отверстия для крепления и установки двигателей, и усиливающих опор.
Кстати о последних. В качестве экономии денежных средств, опоры для направляющих можно было бы не ставить, но так как толщина листа маловата по моему разумению, я посчитал, что такие опоры значительно усилят конструкцию.
Сам портал было решено перемещать, установив две ШВП по краям, а не одну по центру, это хоть и чуть дороже, но зато не надо переживать о весе портала.
После того как основание было готово, я приступил к прорисовке портала. Нарисовал основную балку, которая будет нести на себе портал и перемещать его вдоль всего основания. Балка получилась довольно крепкая за счет параллельных пластин скрепленных и стянутых между собой цилиндрическими осями. Основную плоскость крепления к кареткам сопряг с пластинами, образующими стойки портала. Их усилил листом толщиной 6мм (он у меня тоже в гараже был). Все остальное рисовал так же, как и основание.
Прикрепив к проекту направляющие каретки и ШВП гайку по Y оси, накидал механизм перемещения Z оси. В нем уже использовал Т-образные опоры направляющих, а к направляющим кареткам крепится конечная плита, которая сопрягается со шпинделем.
Хочу сделать маленькое отступление и рассказать про использование мной цилиндрических направляющих. Знаю, что некоторые “специалисты” в комментариях скажут о том, что эти направляющие будут прогибаться, точность будет плохая, жесткость конструкции тоже никакая и все в таком роде. Для обработки тех материалов, по которым этот станок делается и при использовании такого диаметра направляющих, на такую длину как у меня, прогиб будет ничтожен, жесткости более чем достаточно.
Во всей конструкции использовал ШВП диаметром 16мм с шагом 5мм.
После обрисовки силовой рамы станка, добавил к ней несколько вспомогающих элементов, такие как уголки, на которых должен лежать гибкий кабель-канал и опоры, крепящиеся к основанию станка.
Изготовление деталей к станку началось в той же последовательности, в которой их рисовал. Детали из обрезков и листа дюрали я обрабатывал на своем прошлом проекте — станке с ЧПУ. Скажу сразу, если посчитать в общей совокупности, то на обработку всех плоских деталей ушло не более 8 часов. Больше времени потратил на подбор режима резания и ожидание нескольких нужных мне фрез.
В основном использовал фрезу одноперую диаметром 6мм, а также для маленьких отверстий двухперую диаметром 3мм. Конечно же, не обошлось без сломанных фрез, но в конце концов это же опыт, хоть не такой дешёвый как хотелось бы.
Направляющие и хвосты ШВП мне обточили друзья, там тоже не обошлось без косяков. Это все мелочи, такое бывает, когда человек всю жизнь крепко выпивал, а потом резко бросил.
Станок собирался как конструктор, похоже, что в свое время я в них не наигрался и сейчас восполняю это сборкой и конструированием станков. Приятно, когда все детали подходят друг к другу и почти не требуется их дорабатывать и подгонять. Однако дорабатывать все же пришлось. Возникла трудность с сопряжением двигателей и ШВП.
Заказав дополнительно три двигателя аналогичных тому, который у меня уже был, а также 4 муфты для соединения валов двигателей и ШВП. Когда все заказанное пришло, выяснилось, что диаметр выходных валов двигателей 6,2мм, а приехавшие муфты были с отверстиями 8 и 12мм, то, что надо, так как у имевшегося у меня в наличие двигателя выходной вал был 8мм. В итоге я заказал три новых муфты с диаметром 6 и 12мм, после чего я просто рассверлил отверстие до 6,2мм.
Осталось непонятным то, почему вал двигателя на 0,2мм больше и что у них вообще за стандарты такие, или все зависит от конкретного производителя, какой пруток был в наличии такой в качестве вала и решили использовать?
Будьте внимательны при заказах.
Механическая часть почти готова, теперь можно переходить и к электрической. Двигатели подсоединил к драйверам. Два двигателя оси X, подключил параллельно к одному драйверу DM542, другие подсоединил к более дешевым драйверам (без названия) на основе TB6600. Все три драйвера подключил к контроллеру DDCSV2.1 на 4 оси, вот только четвертая ось, именно поворотная, не может быть назначена как дублирующая любой из основных трех. Вместе с контроллером в комплекте шел MPG пульт для ручного управления координатами – крутая штука. Думаю, в дальнейшем она мне не разонравится и будет продолжать меня радовать.
На данный момент сделал навесной монтаж и не протягивал нормальные провода, да и детали еще не все куплены. Фактически подключил для проверки работоспособности механики. На днях только заказал шпиндель воздушного охлаждения на 1,5 кВт. и частотный преобразователь с цангами.
В дальнейшем установлю шпиндель, и буду разводить провода; изготовлю и смонтирую ящик под электронику.
В заключительной части покажу и расскажу, что за зверь у меня такой получился, поговорим о его плюсах и минусах и сделаем выводы.
Источник: https://pikabu.ru/story/stanok_s_chpu_iz_togo_chto_zavalyalos_v_garazhe_6592185